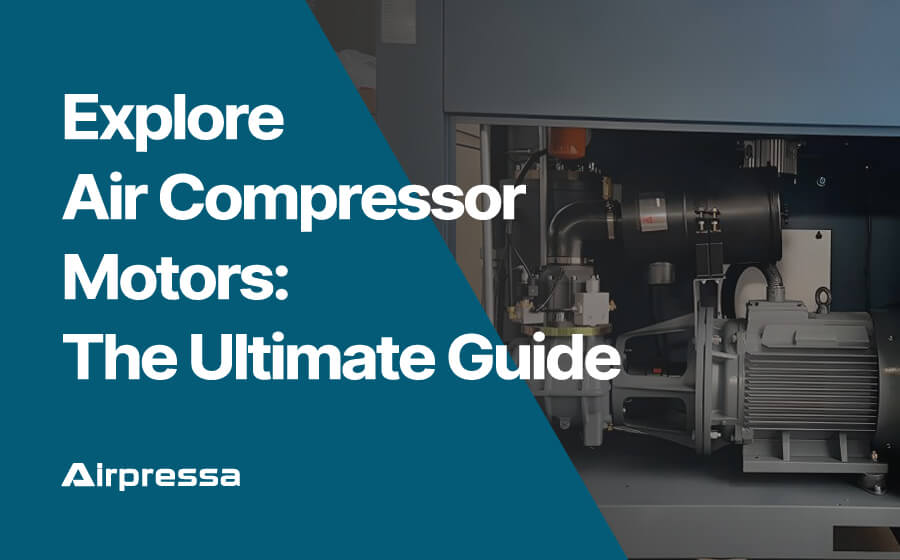
The air compressor motor is the beating heart for a compressor drive system. Air compressors are essential tools in various industries, and their motors are the powerhouse behind their functionality.
This article will take you through everything that air compressor motor and its working principle and types.
Let’s dive in!
You can click on any section that you interest to get there quickly.
The Role of the Motor in Air Compressors
For most air compressors, the motor is the core of its power.
The difference is that diesel compressors rely on a diesel engine to power the air end.
How the Air Compressor Motor Works
The motor’s primary function is to convert electrical energy into mechanical energy, which drives the compressor’s piston or rotor.
The motor’s operation typically involves the following steps:
- Start-Up: When the compressor is switched on, an electric current flows through the motor’s windings, creating a magnetic field.
- Rotational Force: The magnetic field interacts with the motor’s rotor, causing it to rotate.
In the case of a piston compressor, this rotation drives the piston, compressing air. For a rotary screw compressor, it drives the male and female rotors to create compressed air.
- Compression: As the rotor or piston moves, it compresses the incoming air. This compression increases the air pressure and decreases its volume.
- Discharge: The compressed air is then released for various applications. The motor continues to operate to maintain the desired pressure levels.
Air Compressor Motor Types
Compressor motors come in various types, each with specific characteristics that make them suitable for different applications. Here, we’ll explore the most common types:
Single-Phase Motors
Advantages
Cost-Effective: Single-phase motors are generally more affordable, making them suitable for budget-conscious consumers.
Simplicity: They are easy to install and maintain, ideal for small-scale applications.
Widespread Availability: Single-phase power sources are readily available in most settings.
Disadvantages
Lower Starting Torque: These motors might struggle with heavy loads or machinery with high starting torque requirements.
Less Efficient: In terms of power consumption, single-phase motors tend to be less efficient.
Efficiency: Single-phase motors are efficient for lighter tasks and applications but may not be the best choice for continuous or heavy-duty use.
Maintenance Requirements: They generally have low maintenance requirements, making them cost-effective in the long run.
Three-Phase Motors
Advantages
High Efficiency: Three-phase motors are more energy-efficient, which can result in long-term cost savings.
Greater Starting Torque: These motors handle high starting torque machinery with ease.
Durability: Known for their longevity and robust performance, especially in industrial settings.
Disadvantages
Higher Initial Cost: Three-phase motors often come with a higher upfront price tag.
Complex Installation: They require a dedicated three-phase power supply, which may not be available in all locations.
Efficiency: These motors are ideal for heavy-duty and continuous operations, offering excellent efficiency.
Maintenance Requirements: While they may have higher upfront costs, three-phase motors tend to require less maintenance, reducing long-term expenses.
Click to view our three-phase industrial compressors.
Choosing the Right Motor Type
Selecting the right motor type for your air compressor depends on your specific needs. Here are some considerations:
Usage: Determine how you plan to use the air compressor. For occasional or light-duty tasks, a single-phase motor might suffice. For continuous or heavy-duty use, a three-phase motor is a better choice.
Power Supply: Ensure your location has the appropriate power supply for the chosen motor type. Three-phase motors require a three-phase power source.
Maintenance: Consider the maintenance requirements. Induction motors, especially three-phase models, often have lower maintenance needs, providing long-term cost savings.
Cost: Evaluate your budget. While single-phase motors are cost-effective, three-phase motors may have a higher upfront cost but offer better long-term efficiency.
By understanding these motor types and their characteristics, you can make an informed decision when selecting the right air compressor motor for your applications.
Whether you’re running a small workshop or a large industrial facility, choosing the appropriate motor is essential for optimal performance and efficiency.
Proper Sizing of Compressor Motors
Selecting the right motor size for your air compressor is essential to ensure optimal performance, efficiency, and longevity. The process involves considering several critical factors:
Compressor Horsepower Requirements
The motor’s horsepower (HP) should match or exceed the air compressor’s requirements. To determine the required HP, consider the following:
Air Flow Needs: Calculate the cubic feet per minute (CFM) or liters per second (L/s) required for your application. Ensure the motor can generate the necessary airflow.
Pressure Rating: Know the required pounds per square inch (PSI) or bar rating. The motor must deliver the pressure needed for your tools or equipment.
Duty Cycle: Consider how often and for how long the compressor will run. Continuous-duty compressors demand motors capable of prolonged operation without overheating.
Want to know what the compressor duty cycle is and what a reasonable break interval is? Please read this article: What is the Air Compressor Duty Cycle and Its Importance?
What Are Differences Between cfm, m3/min, psi, bar, hp, kw?
Air compressors are essential machines in many industries, and they come in different types and sizes. When choosing an air compressor, it’s important to understand the different measurement units used to describe their performance.
Want to learn more about the differences between 3/min, cfm, psi, bar, hp, and kW?
Voltage and Phase
Verify that your power supply matches the motor’s voltage and phase requirements. Common options are single-phase (typically found in smaller units) and three-phase (commonly used in industrial settings). Ensure your power source can accommodate the motor you choose.
Efficiency Considerations
Look for motors with high energy efficiency ratings to reduce long-term operating costs. Energy-efficient motors can result in substantial savings, especially in applications with frequent and continuous use.
Environmental Conditions
Consider the environment where the compressor will operate. In harsh or hazardous settings, you may need motors with special features like explosion-proof enclosures or resistance to extreme temperatures and moisture.
Maintenance Requirements
Different motors have varying maintenance needs. Choose a motor type that aligns with your maintenance capabilities and expectations.
Properly sizing your air compressor motor ensures not only efficient performance but also the longevity of your equipment.
An underpowered motor will strain to meet the demands, leading to premature wear and tear.
On the other hand, an overpowered motor may waste energy and incur unnecessary costs.
Therefore, taking the time to calculate your requirements and choosing the right-sized motor is a crucial step in the world of air compressors.
Air Compressor Maintenance Checklist: The Ultimate Manual
Throughout this manual, you will find detailed instructions on performance monitoring, visual inspections, checking motor and electrical connections, lubrication, and much more. Each section is carefully crafted to provide practical insights and tips that will help you keep your air compressor in top shape.
Variable Frequency Drive (VFD) Motors for Compressors
One such innovation that has greatly impacted the aerodynamic industry is Variable Frequency Drive (VFD) motors.
These sophisticated motors have transformed the way compressors operate, offering numerous advantages that make them increasingly popular.
VFD motors, also known as adjustable-speed drives.
Inverter Compressors VS Normal Compressors: Which is Better?
They allow for precise control of the motor’s speed, which in turn regulates the compressor’s output. This innovation provides several key advantages:
It has the following advantages
Energy Efficiency
VFD motors are renowned for their energy-saving capabilities. By adjusting the motor’s speed to match the required air output, they eliminate the energy waste associated with constant-speed motors.
This results in significantly reduced electricity bills, making VFD compressors an economically sound choice.
Smooth Start and Stop
VFD motors enable soft starting and stopping of the compressor.
This gentle approach reduces mechanical stress and wear on the motor and other components, extending their lifespan and minimizing maintenance requirements.
Precise Air Output Control
VFD technology allows for precise control of the air output. Whether your application demands a rapid change in pressure or a gradual adjustment, VFD motors can handle it, ensuring that you have the right air pressure when you need it.
Reduced Peak Power Demands
In applications with fluctuating air demands, VFD motors excel. They reduce peak power demand by supplying only the necessary amount of compressed air, further contributing to energy savings.
Lower Operating Costs
With reduced energy consumption, decreased maintenance needs, and extended equipment life, VFD compressors offer a cost-effective solution over the long term.
Environmental Benefits
Using less energy not only lowers costs but also reduces your carbon footprint. VFD motors help companies meet sustainability goals and environmental regulations.
When to Use VFD Motors in Compressors
While VFD motors offer numerous benefits, they may not be suitable for every application. They are most advantageous when:
There are variable air demands: If your air compressor experiences fluctuating demands, such as in applications with varying load sizes or where multiple tools operate simultaneously, VFD motors are an excellent choice.
Energy efficiency is a priority: When reducing energy consumption is a top priority, VFD compressors make sense. They are particularly effective in applications where the compressor operates continuously, allowing for substantial energy savings.
Precise control is required: Some applications demand precise control over air pressure and flow. VFD motors excel in these situations, ensuring that you always have the right amount of compressed air.
Variable frequency drive (VFD) motors can save energy, enhance control, and reduce maintenance costs makes them a compelling choice for many applications.
However, it’s crucial to assess your specific needs and air compressor usage to determine whether VFD motors are the right fit for your situation.
What is the VSD Compressor and How to Choose Correctly
Want to know more about VSD air compressor? Click to learn more:
- What is the VSD Compressor?
- What is the VFD in the VSD Compressor?
- The Difference between VSD and Fixed-Speed Compressor
- Features and Benefits of the VSD Compressor
- Costs and Operations: VSD Compressor vs. Fixed Speed Compressor
- How to Choose the Right VSD Air Compressor?
Motor Voltage and Phase Considerations
Air compressor motors come in various voltage and phase configurations, and choosing the right one is paramount for efficient and safe operation. Here’s why motor voltage and phase considerations are crucial:
Voltage Compatibility
Safety: Ensuring the motor voltage matches the power supply voltage is a fundamental safety measure. Mismatched voltages can lead to electrical hazards and damage to the motor.
Optimal Performance: A motor operating at its rated voltage delivers optimal performance. Operating outside this range can lead to inefficiency and reduced motor life.
Motor Longevity: Correct voltage helps prevent overheating and overloading, which can extend the motor’s lifespan.
Phase Configuration
Phase and Power Supply: The most common phase configurations are single-phase and three-phase. Matching the motor’s phase with the power supply is vital. Running a three-phase motor on a single-phase supply, for example, can cause damage and inefficiency.
Efficiency: Three-phase motors generally provide better efficiency and power factor compared to single-phase motors. Selecting the appropriate phase ensures your compressor operates at peak efficiency.
Selecting the Correct Voltage and Phase
Choosing the right motor voltage and phase configuration can be broken down into the following steps:
- Check Your Power Supply: Identify the voltage and phase of your facility’s power supply. This information is typically available on your electrical panel.
- Motor Data Plate: Examine the motor’s data plate, which provides essential details, including voltage and phase requirements. Ensure it matches your power supply.
- Consult the Manufacturer: If you’re unsure or have unique requirements, consult the air compressor manufacturer or an electrician. They can help you make the right selection.
Matching the motor’s requirements to your power supply not only ensures the compressor’s performance but also extends its lifespan and reduces the risk of electrical issues.
Whether you’re setting up a new compressor or replacing a motor, always make the correct voltage and phase configuration a top priority.
Contact our technical team support on voltage, frequency, phase, operating pressure, airflow and more. To choose the most suitable air compressor