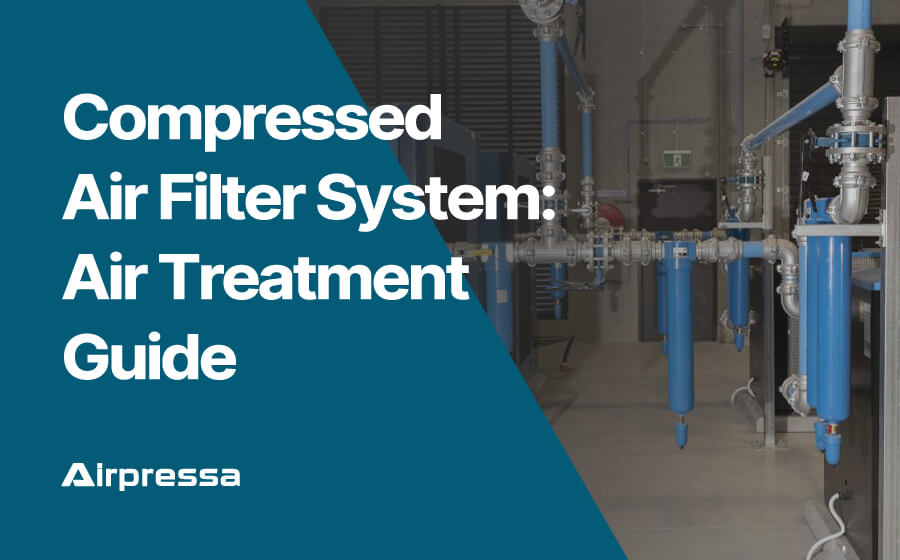
The compressed air filter system is an essential component of almost every air compression system. As an important air treatment system, it can provide cleaner aerodynamics for manufacturing and projects.
You can click on any section that you interest to get there quickly.
What Is the Compressed Air Filter System?
The compressed air filter system, also known as inline compressed air filter dryer, is an essential component in air compressor system. Its main function is to eliminate water vapor and any harmful substances from the compressed air before it reaches the point of use.
When air is compressed, the temperature rises and the ability of air to hold water vapor increases. As the compressed air cools down, the vapor turns into condensation, which can potentially cause extensive damage to the system and the tools it powers.
This is where the filter system comes into play. It effectively removes the condensation, as well as particles, oils, and other contaminants, ensuring you get dry, clean compressed air for your application.
This prevents rust and corrosion within the compressor and its distribution system, and ensures the efficient and reliable operation of the compressor and pneumatic tools.
How Do Air Filters Work?
The working process of the compressed air filter system is not complicated and mainly consists of the following steps:
Filtration Stages
The inline compressed air filter system typically consists of multiple filtration stages, each designed to target specific contaminants at different levels of granularity.
The initial stages address larger particles, preventing them from progressing further and potentially causing damage to downstream components.
Particulate Removal
In the first stage, the filter captures solid contaminants such as dust, rust, and debris present in the compressed air. This prevents these particles from reaching tools and equipment, ensuring their optimal performance and longevity.
Coalescing Filtration
The coalescing filter, situated in subsequent stages, focuses on finer particles and aerosols. It utilizes specialized media to merge microscopic water droplets and oil mist into larger droplets, facilitating their removal from the air stream.
Adsorption of Vapors
Some advanced air filter systems incorporate adsorption media, such as activated carbon, to capture and remove vaporous contaminants. This is particularly important in applications where air purity is critical, such as pharmaceutical or food processing.
Compressed Air Filter Dryer
Air filter systems often integrate the air dryer to address moisture content. This can involve desiccant materials that absorb and trap water vapor, preventing it from causing corrosion or impairing the functionality of downstream equipment.
What Is The Compressed Air Dryer? A Comprehensive Overview
The compressed air dryer is an important part of air compression system, it ensures the quality and efficiency of compressed air systems.
Let’s delve into what a compressed air dryer is and why it’s a crucial component in various industries.
Compressor Auto Drain
Many compressed air filter systems are equipped with auto drain to expel collected contaminants and moisture. This ensures continuous and efficient operation without the need for manual intervention.
Pressure Drop Monitoring
Some air filters equipped with a pressure monitoring gauge, to pressure drop across the filter elements is monitored to indicate the level of contamination. An increase in pressure drop signals the need for maintenance and replacement of filter elements.
Compressed Air Filter Types
Compressed air filters come in several types, each designed to remove specific types of contaminants from the compressed air. The primary types include:
Particulate Filters
These filters primarily remove solid particles such as dust, pollen, and various types of dirt. They’re typically used where high purity air is required and can catch particles down to 1 micron in size.
Coalescing Filters (Oil Removal Filters)
They can capture and remove oil aerosols that could contaminate the compressed air system. They’re often used in conjunction with particulate filters to provide cleaner air.
The unique element design causes aerosols to coalesce, or come together, forming larger droplets that can be drained away.
Oil Vapor Removal Filters (Activated Carbon)
These filters will remove oil vapor and organic solvents. Activated carbon within the filter attracts these vapors which adsorb onto the surface of the carbon.
Dry Particulate Filters
These filters are beneficial in systems that have implemented drying technologies such as desiccant air dryers. They help in capturing desiccant dust particles.
Each type of filter plays a specific role in ensuring the cleanest, driest air possible.
Usually, the entire inline compressed air filter system contains multiple different types of air filters to intercept a variety of pollutants.
Two Key Parameters of Compressed Air Filter Systems
The effective functioning of compressed air filter systems is largely dependent on two crucial parameters:
Compressed Air Filter Sizes (Processing Air Capacity)
The processing air capacity, or flow rate, of a compressed air filter represents its capability to handle a certain volume of compressed air. This is usually denoted in cubic meters per minute or cubic feet per minute (cfm).
Here are the processing air capacities of several common models of compressed air filters:
– 015 Model: Capable of processing 15 m³/min of compressed air.
– 025 Model: Exhibits the capacity to handle 25 m³/min of compressed air.
– 035 Model: Designed to manage an air volume of 35 m³/min.
– 060 Model: Processes a notable volume of 60 m³/min.
– 090 Model: Known for its ability to handle a whopping 90 m³/min of compressed air.
– 120 Model: Another high-performing option, offering a capacity of 120 m³/min.
– 150 Model: Often the choice for large-scale operations, this model impresses with a capacity of 150 m³/min.
The right capacity adds value to your operations by ensuring your equipment runs smoothly and optimally.
Each air compressor manufacturer or compressed air system supplier may provide different model codes, please consult them for details.
The Accuracy of Dust and Oil Removal
The filtration accuracy of a filter outlines its ability to trap particles, measured in micrometers (um) and oil elements, quantified in parts per million (ppm).
‘Q’ Grade Filters: They can eliminate solid particles sized 3.0 um and can separate residual oil content down to 1.0 ppm.
‘P’ Grade Filters: These models can handle particle sizes down to 3.0 um and limit oil elements to 0.1 ppm.
‘M’ Grade Filters: High on the accuracy scale, these filters deal with particles as tiny as 1 um and achieve oil residual levels as low as 0.1 ppm.
‘S’ Grade Filters: With an ability to eliminate particles of 0.1 um size, these filters stand out in limiting oil concentrations to only 0.05ppm.
‘H’ Grade Filters: Outclassing many peers, they’re capable of filtering out 0.01 um and maintaining a virtually oil-less condition of 0.01 ppm of oil residual.
Usually, they are used in combination, such as Q, P, S, as a system, or P, S, M ,H*2 as a whole air filter system.
How to Choose the Right Compressed Air Filter System?
Selecting the right compressed air filter system can seem like a daunting task. Multiple factors come into play, including the type of filter, processing capacity, and filtration class.
Here are 3 tips to help you make an appropriate choice.
1. Determine the Type of Air Filter
The first step is to identify the type of air filter that suits your needs best. Are you looking to remove particulates, or is oil aerosol your primary concern?
Maybe you need to filter out oil vapor, high-temperature air, or desiccant dust. Your specific operational needs will determine the type of filter you should go for.
2. Confirm Processing Air Capacity
Assess the air flow volume of your operational compressor. The processing air capacity of the filter system should match or exceed the volume of air your compressor generates.
This ensures that the filter can effectively handle the quantity of air passing through it, preventing any drop in performance.
An under-performing filter might not adequately clean the air, whereas an over-performing filter could add unnecessary cost to your operation.
3. Confirm the Accuracy of Dust and Oil Removal
Once you have determined the type of filter and confirmed your capacity needs, the next step is to establish the appropriate filtration class. Different industries require different grades of filtration. Here are some examples:
Construction Industry: The construction industry often contends with high levels of solid particulates. Therefore, a ‘Q’ or ‘P’ class filter, which are efficient for removing solid particles, would be an optimal choice.
General Manufacturers: Depending upon the specific manufacturing process, a ‘P’ or ‘S’ class filter should provide an acceptable level of filtration. It strikes a balance between cost-effectiveness and the filtration of commonly encountered contaminants.
Prevention and Control Industry: This industry typically requires a higher standard of filtration. ‘M’ or ‘S’ class filters are often employed to ensure a clean and healthy environment.
Glass Container Industry: The production of glass requires extremely clean air. ‘M’ or ‘T’ class filters are usually utilized in these settings.
Food, Medical, and Hygiene Industries: These sectors mandate the strictest level of cleanliness. High grade filters like the ‘T’ or ‘H’ class are generally recommended. Moreover, in these industries, oil-free compressors are a better choice.
How to Install Compressed Air Filter System Correctly
Installing a compressed air filter system is a crucial step to ensure the quality and efficiency of your compressed air supply.
Follow these steps for a correct installation process:
1. Choose the Right Location
Select an installation site that is easily accessible for maintenance and away from potential contaminants. Ensure proper ventilation and adequate space for the filter system.
2. Install a Prefilter
Before the main filter, consider installing a prefilter to capture larger particles, such as Q grade air filter. This step extends the life of the primary filter and enhances the overall filtration efficiency.
3. Check the Air Flow Direction
Most filters are designed to operate in a specific flow direction. Ensure that the arrows indicating the flow direction on the filter housing align with the direction of compressed air flow.
Incorrect installation can compromise filtration efficiency.
4. Install Differential Pressure Gauges
Differential pressure gauges help monitor the condition of the filter elements. Install gauges before and after the filter to measure pressure drop.
Replace the filter elements when a significant pressure drop is observed.
5. Ensure Proper Sealing
Use appropriate sealants and follow the manufacturer’s guidelines for sealing connections.
Inspect and ensure a tight seal at all connection points. Leakage will not only significantly reduce the efficiency of the filtration system, but also waste the air output of the compressor, reduce production efficiency, and waste electricity and funding.
6. Consider Condensate Drains
Apart from these steps, if your air filter system includes condensate drains, ensure they are correctly installed.
Compressed auto drains can enhance the efficiency of the system by periodically removing accumulated moisture.
7. Connect to the Air Intake
This is where your air tool will connect to receive clean compressed air. The connection should be tight and secure to prevent leaks. Ensure that it’s aligned well to avoid unnecessary strain on the hose.
8. Test the Compressed Air Filter System
Before putting the system into full operation, perform a comprehensive check.
After you’ve connected the filter, it’s critical to test the whole compressed air system. Activate your air compressor and watch the behavior of the system carefully. Listen for strange noises, monitor the pressure levels, and check for air leaks.
Last but not least, regular maintenance and timely replacement of the compressed air filter system and element, this includes:
- Seal and connection checks
- Pressure differential checks
- Scheduled replacement of compressed air filter elements
- Condensate drainage maintenance
- Air quality resting