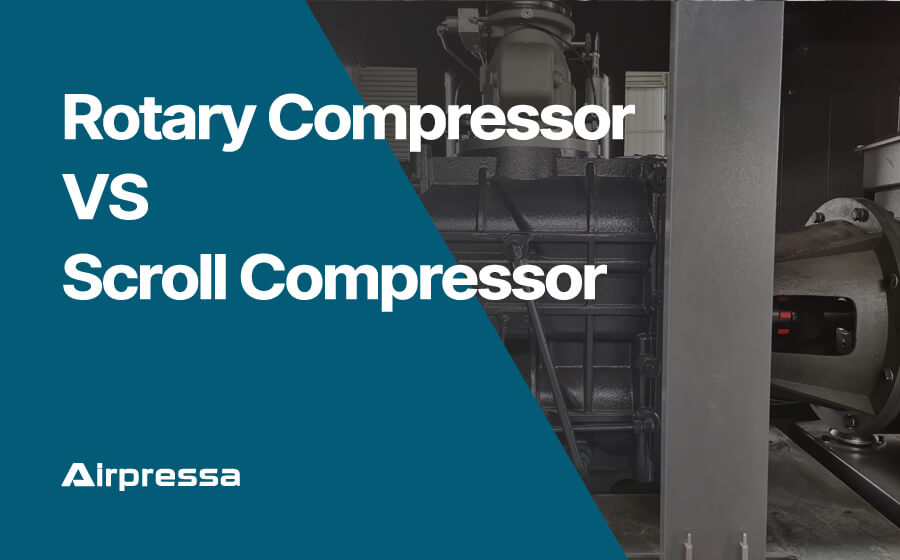
The debate between rotary compressors and scroll compressors has long been a topic of discussion. Both offer unique advantages and are widely used in various industries.
In this article, we will delve into the key differences and benefits of these two compressor types, helping you make an informed decision for your specific needs.
You can click on any section that you interest to get there quickly.
They Work on Different Principles
How Does the Rotary Screw Compressor Work
The rotary compressor operates on the principle of positive displacement. It utilizes a pair of rotating helical screws, known as rotors, housed within a compression chamber.
The rotors are precisely machined with helical lobes that intermesh with each other, forming a series of compression pockets. As the rotors rotate, the volume of these pockets decreases, compressing the air trapped inside.
The process begins when atmospheric air enters the compressor through an inlet port. The rotating screws then draw in the air, which gets progressively compressed as it moves along the rotors’ length.
As the air is compressed, its pressure and temperature rise. The intermeshing lobes of the rotors ensure a tight seal, preventing any backflow and optimizing compression efficiency.
To facilitate smooth operation and reduce friction, the rotors require precise alignment and close tolerances. This is achieved through the use of high-quality bearings and a robust lubrication system.
The lubricant not only minimizes friction but also helps in dissipating the generated heat, ensuring reliable performance and longevity of the compressor.
Once the air reaches the end of the rotors, it exits the compression chamber through a discharge port. It is then directed to the air tank or directly to the application, depending on the specific system configuration.
How Does the scroll compressor work
The scroll compressor consists of two interlocking spiral-shaped scrolls, aptly named the fixed scroll and the orbiting scroll. These scrolls are usually made of high-strength materials like stainless steel or aluminum.
The fixed scroll remains stationary while the orbiting scroll moves in an eccentric motion, creating a series of gas pockets or chambers between them.
The compression process begins as the orbiting scroll rotates, causing the gas or air to be drawn into the outermost chamber. As the orbiting scroll continues its rotational movement, the gas is gradually compressed towards the center of the scroll set.
The inward movement reduces the volume of the gas, resulting in an increase in pressure. The compressed air is then discharged through an outlet port located at the center of the scrolls.
The interlocking scrolls create a continuous seal, eliminating the need for piston rings or valves. This design reduces internal leakage and minimizes energy loss, enhancing overall efficiency.
Pros and Cons of Rotary Compressors and Scroll Compressors
Rotary Compressors
Advantages
Rotary compressors offer several key advantages in the realm of air compression.
Firstly, rotary compressors are known for their high efficiency.
Their positive displacement design allows for a continuous flow of compressed air, ensuring a steady supply for various applications. This efficiency translates into lower energy consumption, resulting in cost savings for users.
Secondly, another notable advantage of the rotary compressor is its continuous operation.
Their design enables them to handle larger capacities, making them suitable for industrial operations that require substantial air output.
Additionally, rotary compressors are compact in size and have a relatively simple construction. This makes them easy to install and maintain, reducing downtime and operational costs for users.
Disadvantages
Despite their many advantages, rotary compressors also have a few limitations.
One drawback is their higher initial cost compared to other types of compressors. The precision engineering required for their design, along with the need for quality components, contributes to the higher price tag.
Besides, rotary compressors will generate more heat during operation compared to other compressors. Proper cooling mechanisms, such as effective ventilation or cooling systems, need to be in place to manage the temperature rise adequately.
And most of the time, the screw compressor needs to be used with an air dryer, such as the refrigerated air dryer.
Scroll Compressors
Advantages
High Efficiency: Scroll compressors are known for their excellent energy efficiency, delivering optimal performance while minimizing energy consumption. This can result in significant cost savings for businesses in the long run.
Quiet Operation: Compared to other types of compressors, scroll compressors operate with reduced noise levels. This makes them suitable for environments where noise pollution needs to be minimized, such as offices or residential areas.
Compact Design: Scroll compressors feature a compact and lightweight design, allowing for easy installation in space-constrained areas. Their small footprint makes them ideal for applications with limited space availability.
Fewer Moving Parts: Scroll compressors have a simplified construction with fewer moving parts, resulting in reduced maintenance requirements and enhanced reliability. This translates to lower maintenance costs and less downtime for businesses.
Disadvantages
Limited Capacity Range: Scroll compressors are best suited for low to medium capacity applications. In high-capacity demands, multiple scroll compressors may be required, increasing the initial investment and complexity of the system.
Sensitivity to Contaminants: Scroll compressors are sensitive to contaminants such as dirt, moisture, and debris. Proper filtration and regular maintenance are necessary to ensure their longevity and optimal performance.
Cost: Compared to some other compressor types, scroll compressors can have a higher initial cost. However, the long-term energy savings and reliability may offset the initial investment.
Limited Modulation Range: Scroll compressors may have limitations in their modulation range, making it challenging to match varying air demand precisely. This can be a consideration in applications where precise control over air output is crucial.
Exploring Rotary vs Scroll Compressors on Performance
Rotary and scroll compressors are two popular options in the air compressor filed. These two types differ in design and functionality, each offering unique advantages.
Stability and Reliability
Both rotary and scroll compressors are known for their stability and reliability in operation.
However, rotary compressors, with their robust construction and simple design, are often preferred in industrial settings where continuous and demanding applications are commonplace.
The rotary design allows for smooth and steady compression, ensuring reliable performance even under heavy workloads.
On the other hand, scroll compressors excel in applications that require consistent and low-to-medium air volumes.
Their design minimizes the number of moving parts, reducing the likelihood of mechanical failures and increasing overall system reliability.
Efficiency
Rotary compressors with their positive displacement design, they can offer high efficiency across a wide range of operating conditions.
This allows for optimal performance in various applications, resulting in lower energy consumption and reduced operational costs.
Scroll compressors, with their unique scroll configuration, deliver excellent efficiency at lower capacities.
They are particularly efficient in maintaining stable air pressure during operation, making them suitable for applications that require steady and precise airflow.
Energy Savings
Rotary compressors excel in energy-saving area, thanks to their ability to deliver compressed air efficiently.
Their positive displacement design allows for precise control of air output, minimizing energy wastage and ensuring energy savings over the long term.
Scroll compressors also offer energy-saving benefits, especially in applications with varying air demand.
Their modulation capabilities allow them to adjust output according to the required airflow, avoiding excessive energy consumption during periods of low demand.
Continuous Operation
For applications that require continuous operation, rotary compressors are often the preferred choice.
Their design allows for uninterrupted and continuous airflow, making them suitable for industries that rely on consistent compressed air supply.
Scroll compressors may have limitations when it comes to continuous operation.
Their intermittent compression process may result in slight fluctuations in airflow, making them better suited for applications that do not require continuous and uninterrupted air supply.
Noise Level
In this regard, scroll compressors have an advantage.
With fewer moving parts and smooth operation contributes to significantly lower noise and vibration levels.
Lower noise makes scroll compressors ideal for noise-sensitive environments such as hospitals, offices, and residential settings.
On the other hand, although may generate more noise and vibration during operation, rotary compressors generally more reliable and suitable for industrial applications
Proper noise insulation and soundproofing measures should be considered when using rotary compressors in noise-sensitive areas.
Which Air Compressor is Right for You: Rotary or Scroll?
In this section, we will explore the factors that can help you decide between a rotary compressor and a scroll compressor, ensuring that you make an informed decision tailored to your specific needs.
Depends on Different Applications and Flow
The choice between a rotary compressor and a scroll compressor largely depends on the intended application.
With the robust construction and ability to handle high air volumes, rotary compressors are well-suited for heavy-duty industrial applications. They are ideal for tasks that require continuous operation and a consistent supply of compressed air, such as manufacturing processes, construction sites, and automotive workshops.
Two-stage rotary compressors with the best industrial performance are the first choice for large manufacturing industries.
You can click here to check Twin Rotary Compressor VS Single Rotary
While not as suitable for high-demand applications, scroll compressors excel in applications that demand precise and stable airflow, making them suitable for industries such as electronics, food and beverage, air conditioning systems, clean rooms, and laboratories.
Purchase Cost
The initial investment cost is an important consideration for any business.
Rotary compressors typically have a higher upfront cost compared to scroll compressors due to their larger size, more complex design, and ability to handle heavier workloads.
Scroll compressors are generally more compact, simpler in design, and have lower initial costs. They are suitable for applications with lower air volume demands and where cost savings in equipment procurement are a priority.
Electricity Costs
Energy consumption and maintenance requirements are ongoing expenses to consider.
With high efficiency and ability to handle heavy workloads, rotary compressors offer excellent energy-saving potential. They can be designed for optimal performance in demanding applications, resulting in lower energy consumption and reduced electricity costs over time.
It is worth mentioning that the power consumption of large-scale industrial screw air compressors is astonishing.
Fortunately, with the maturity of permanent magnet frequency conversion technology, rotary screw type variable speed air compressors can save energy costs beyond imagination for heavy duty industrial production.
Scroll compressors are also known for their energy efficiency, especially in applications with varying air demand.
Their ability to modulate output according to the required airflow helps minimize energy wastage during periods of low demand, contributing to significant energy savings.
Maintenance Costs
In terms of maintenance, both types of compressors require regular servicing and upkeep.
However, rotary compressors may require more frequent maintenance due to their complex design and higher workload capacity.
In conclusion
Choosing the right compressor depends on various factors including the application requirements, gas volume demands, purchase cost, and ongoing electricity and maintenance costs.
By considering these aspects, you can make an informed decision that aligns with your specific needs and maximizes the efficiency and productivity of your operations.