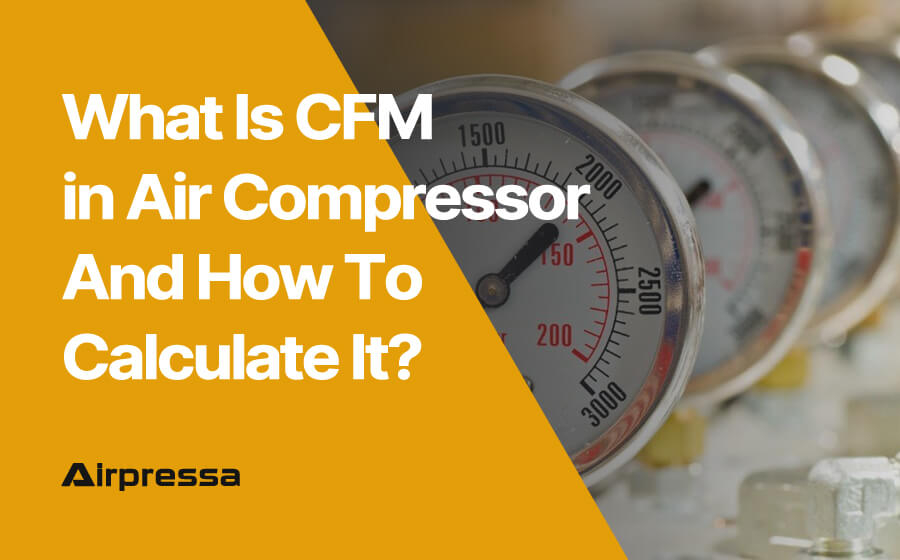
CFM is a crucial factor in determining the performance and efficiency of air compressors. Understanding how to calculate it is essential for selecting the right compressor for your specific needs.
In this guide, we’ll break down the concept of CFM in air compressors in simple terms, provide practical examples and tips on how to calculate it.
You can click on any section that you interest to get there quickly.
What Is CFM in Air Compressor Field?
When it comes to choosing an air compressor, one of the most important specifications to consider is the CFM rating. What is the cfm meaning in air compressor?
CFM(Cubic Feet per Minute) is a measure of the air flow rate that an air compressor can deliver.
Simply put, CFM is a measure of the volume of air that an air compressor can produce at a given pressure. It is typically measured in cubic feet per minute, and it represents the amount of air that the compressor can deliver at a specific pressure level.
The CFM rating of an air compressor is determined by a variety of factors, including the size of the compressor, the size of the motor, and the design of the compressor.
How Important Is CFM for An Air Compressor?
One of the most important things to understand about CFM is that it is directly related to the power and performance of an air compressor.
The higher the CFM rating of a compressor, the more air it can deliver at a given pressure, and the more powerful it will be. This makes CFM a critical factor to consider when selecting an air compressor for any application.
When it comes to air compressors, there are two main types of CFM ratings:
- Free air delivery (FAD)
- Displacement CFM
Displacement CFM is a measure of the total volume of air that the compressor can theoretically produce, while FAD is a measure of the actual volume of air that the compressor can deliver at a specific pressure level.
FAD is typically the more important CFM rating to consider, as it represents the actual performance of the compressor in real-world applications.
In addition to the CFM rating, there are a number of other factors to consider when selecting an air compressor, including the pressure rating, the duty cycle, and the type of compressor (e.g. reciprocating, rotary screw, or centrifugal).
Ultimately, the right air compressor for your needs will depend on a variety of factors, including the specific application, the required air flow rate, and the available power source.
In conclusion, CFM is a critical specification to consider when selecting an air compressor, as it directly affects the power and performance of the compressor.
Whether you are using an air compressor for automotive, industrial, or residential applications, understanding the CFM rating and how it relates to your specific needs is essential for choosing the right compressor for your needs.
What Size CFM Air Compressor Do I Need?
Understanding how to calculate the CFM of an air compressor is essential for choosing the right compressor for your needs.
How to Calculate the CFM?
To begin, you’ll need to know the tools and equipment you plan to use with your compressor, as well as their CFM requirements. Once you have that information, you can use the following formula to calculate the total CFM you need:
Total CFM = CFM of all tools + (CFM x number of tools used at the same time x 1.5)
The “1.5” in the formula represents the fact that most tools require a brief surge of air when they start up, so you’ll need to factor in a bit of extra capacity to compensate for this.
Let’s say, for example, that you plan to use a spray gun that requires 6 CFM, a sander that requires 8 CFM, and an impact wrench that requires 10 CFM. If you plan to use all three tools at the same time, you’ll need a compressor with a total CFM of:
Total CFM = 6 + (8 x 1.5) + (10 x 1.5) = 27 CFM
It’s important to note that this formula provides a rough estimate of the CFM you need. If you plan to use your compressor frequently or for extended periods, you may want to choose a compressor with a slightly higher CFM rating to ensure it can handle the workload.
Another factor to consider when choosing a compressor is the duty cycle, or the amount of time the compressor can operate continuously.
For example, a rotary screw air compressor with a duty cycle of 50% can operate for 30 minutes out of an hour before it needs to rest and cool down. A compressor with a higher duty cycle is generally better suited for industrial or commercial applications where it will be used frequently.
In addition to CFM and duty cycle, other factors to consider when choosing a compressor include the horsepower of the motor, the tank size, and the type of compressor (e.g. piston, rotary screw, etc.).
By carefully considering all of these factors, you can choose an air compressor that meets your needs and provides reliable performance for years to come.
You can check the cfm to m3/min chart.
What Happens If CFM Is too Low?
If the CFM is too low, it can have a significant impact on the compressor’s performance and efficiency.
One of the most significant issues that can occur when the CFM is too low is that the compressor may not be able to provide enough air to power the tools or equipment it is connected to.
For example, if the compressor is being used to power a spray gun, a low CFM can result in poor quality finishes due to insufficient air pressure. This can lead to wasted materials and the need for additional finishing work.
Another issue that can arise from low CFM is that the compressor may become overworked and overheat, causing damage to the motor or other components.
When the compressor is working hard to maintain the required pressure, it may start to overheat due to the increased load. Over time, this can cause damage to the motor or other components, leading to expensive repairs or even the need to replace the entire unit.
In addition to these issues, a compressor with low CFM may also suffer from reduced efficiency and increased energy costs.
When the compressor is struggling to maintain the required pressure, it will need to work harder and consume more energy to keep up with demand. This can lead to higher energy bills and increased wear and tear on the compressor.
To avoid these issues, it’s essential to choose an air compressor with the right CFM for the intended application. It’s also important to regularly maintain the compressor to ensure it continues to operate at optimal levels. This can include regular oil changes, filter replacements, and keeping the compressor clean and free of debris.
So, if the CFM in air compressor is too low, it can lead to poor performance, overheating, increased energy costs, and other issues.
By choosing the right compressor for the intended application and regularly maintaining it, you can ensure optimal performance and longevity of your equipment.
How Do I Increase the CFM in Air Compressor?
If you are using an air compressor, you might come across a time where you need to increase the CFM (cubic feet per minute) of your compressor. Such as using larger pneumatic tools or painting large surfaces.
Besides purchasing air compressors with larger CFM, are there any other solutions? Here are some suggestions, but please be careful to follow the guidance of a professional engineer:
Increase the tank size
One of the most effective ways to increase the CFM of your compressor is to increase the size of the air tank.
A larger tank can store more compressed air, which means you can use your tools for a longer time before the compressor has to kick in and refill the tank.
Increase the pressure
Increasing the pressure of your compressor will also help to increase the CFM output. You can check the maximum pressure rating of your compressor and set it to the highest pressure possible.
However, be cautious, and do not exceed the pressure limit to avoid potential damage to your compressor and tools.
Change the compressor pump
If your compressor is a single-stage unit, it might be worth upgrading to a two-stage compressor pump.
The two-stage compressor pump compresses the air twice, resulting in a higher CFM output. This type of compressor pump is more efficient for heavy-duty applications that require a higher CFM output.
Increase the horsepower
Increasing the horsepower of your compressor is another way to boost the CFM output. A higher horsepower motor will provide more power to the compressor, enabling it to compress more air per minute, thus increasing the CFM.
However, be mindful that increasing horsepower will also consume more energy, so make sure you have a powerful enough electrical supply to handle the increase.
Upgrade the air filter and intake system
A dirty air filter or a restricted intake system can cause the compressor to work harder and restrict airflow, which will decrease the CFM output.
You can upgrade to a high-quality air filter or intake system can improve the airflow and increase the CFM output.
In conclusion
Increasing the tank size, pressure, upgrading the compressor pump, increasing horsepower, and upgrading the air filter and intake system are all effective ways to increase the CFM output of your compressor.
Remember, it is essential to keep your compressor well-maintained and to follow the manufacturer’s instructions to prevent any damage and ensure long-lasting performance.