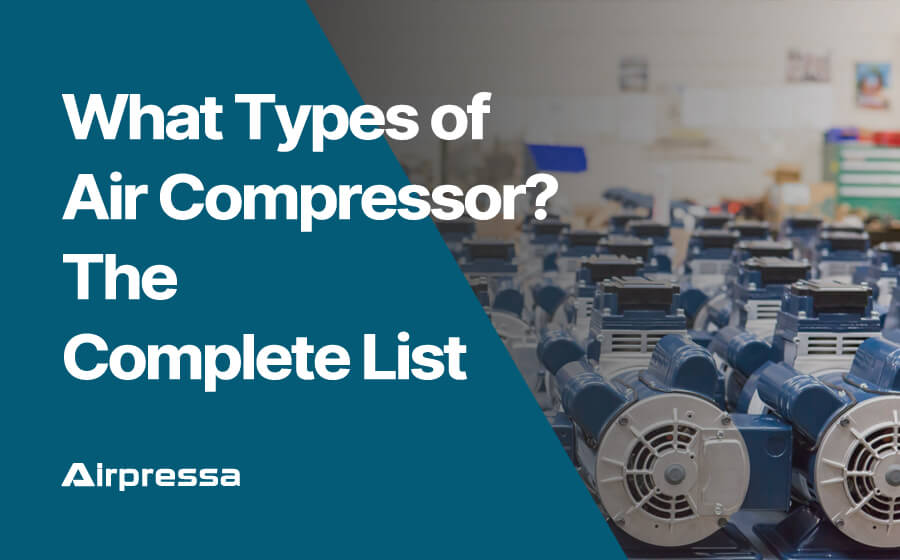
There are many types of air compressor, positive and dynamic air compressors are two main types, each with its own advantages and applications.
Positive air compressors rely on positive displacement to deliver a continuous flow of compressed air, while dynamic air compressors use high-speed impellers to achieve compression.
Understanding the differences between these compressor types can help industries choose the most suitable comp1ressor for their specific needs.
You can click on any section that you interest to get there quickly.
Positive Air Compressor
What is the Positive Air Compressor?
Positive air compressors are a type of air compressor that works on the principle of positive displacement. These compressors trap a fixed volume of air and then reduce the volume to increase its pressure. The compression process is achieved using mechanical components such as pistons, screws, vanes, or scrolls.
Positive air compressors deliver a continuous and steady flow of compressed air, making them suitable for applications that require a consistent air supply.
What types of air compressors does it include?
There are several types of positive air compressors, each with its unique design and applications.
With the segmental development and verification of the air compressor industry, in the general manufacturing, mining, food, pharmaceutical, medical and other industries, the following main volumetric air compressors occupy a dominant position in the market.
- Reciprocating air compressor
- Rotary screw air compressor
- Rotary vane air compressor
- Scroll air compressor
They will be the focus of discussion in this article.
There are also less common types:
- Rotary lobe air compressor
- Liquid ring air compressor
Let’s dig deeper!
Reciprocating Air Compressor
What is the Reciprocating Air Compressor?
The reciprocating air compressor, also known as a piston compressor, falls under the category of positive displacement compressors.
It operates using the principle of reciprocation, where a piston moves back and forth within a cylinder to compress the air.
Reciprocating compressors are available in both single-stage and two-stage configurations.
Single-stage compressors compress the air in one stroke, while two-stage compressors perform an initial compression in one cylinder and then send the partially compressed air to a smaller cylinder for further compression.
How Does it Work?
The working of a reciprocating air compressor involves a series of stages. When the motor starts, it drives the piston to move downward, creating a vacuum in the cylinder. Atmospheric air rushes in to fill the void, and when the piston moves upward, it compresses the air.
In single-stage reciprocating compressors, the compressed air is discharged directly into the storage tank or downstream application. In two-stage compressors, the partially compressed air from the first cylinder is further compressed in the second stage to achieve higher pressures.
Reciprocating compressors can be either lubricated with oil or oil-free, depending on the specific application requirements
Advantages of Reciprocating Air Compressors
Reciprocating air compressors offer several advantages, making them a popular choice in various industries:
Versatility: Reciprocating compressors are versatile and suitable for a wide range of applications, from small workshops to large industrial settings.
High Efficiency: When properly maintained, reciprocating compressors can achieve high levels of efficiency, providing cost-effective compressed air solutions.
Pressure Adjustability: Operators can adjust the pressure output of reciprocating compressors to meet the specific needs of different applications.
Durability: With robust construction and fewer moving parts, reciprocating compressors are known for their durability and long service life.
Industries Where Reciprocating Air Compressors are Used Reciprocating air compressors find application in various industries due to their flexibility and reliability:
Automotive: In the automotive industry, they are used for pneumatic tools, tire inflation, and painting applications.
Manufacturing: Reciprocating compressors power pneumatic machinery and assembly lines in manufacturing plants.
Construction: They are essential for operating pneumatic tools on construction sites.
Agriculture: Reciprocating compressors aid in crop spraying and other agricultural applications.
Service and Maintenance: They are used in repair shops and service centers for equipment maintenance.
The reciprocating air compressor is a versatile and efficient tool widely utilized in diverse industries. Its reciprocating motion, adjustability, and durability make it a preferred choice for various applications.
Rotary Screw Air Compressor
What is the Rotary Screw Air Compressor?
The rotary screw air compressor is a type of compressor that operates using the principle of two interlocking helical rotors.
These rotors rotate in opposite directions, trapping and compressing the air between them. This continuous rotary motion enables a steady flow of compressed air without pulsations.
Unlike reciprocating compressors, which use pistons for compression, rotary screw compressors provide a smoother and more continuous output of compressed air. They are widely used in various industrial applications due to their efficiency and reliability.
How Does it Work?
The working of a rotary screw air compressor involves two main components: the male rotor and the female rotor. As the rotors rotate, air is drawn into the compression chamber. The helical design of the rotors reduces the volume of the air as it moves towards the discharge port. This compression process results in a continuous flow of compressed air at the desired pressure.
Some rotary screw compressors use oil for lubrication, creating a sealing and cooling effect between the rotors. These are known as oil-injected rotary screw compressors.
On the other hand, oil-free rotary screw compressors use other methods, such as precision manufacturing and specialized coatings, to maintain the clearances between the rotors without the need for lubricating oil.
Advantages of Rotary Screw Air Compressors
Rotary screw air compressors offer several advantages that make them popular in various industries:
High Efficiency: The continuous rotary motion allows for a steady output of compressed air, minimizing energy losses and improving overall efficiency.
Low Noise Levels: Rotary screw compressors are designed for quiet operation, making them suitable for noise-sensitive environments.
Compact Design: They have a compact footprint, saving valuable floor space in industrial settings.
Reduced Maintenance: Compared to reciprocating compressors, rotary screw compressors have fewer moving parts, resulting in lower maintenance requirements.
Versatility: Rotary screw compressors can handle a wide range of air demands, from small workshops to large-scale industrial operations.
Industries Where Rotary Screw Air Compressors are Used
Rotary screw air compressors find application in various industries due to their efficiency and reliability:
Manufacturing: They power pneumatic machinery, control systems, and assembly lines in manufacturing plants.
Construction: Rotary screw compressors are used for various construction tasks, such as operating pneumatic tools and providing compressed air to equipment.
Food and Beverage: They are employed for packaging, cooling, and cleaning processes in the food and beverage industry.
Pharmaceuticals: In pharmaceutical manufacturing, rotary screw compressors are used for material handling and other critical processes.
Automotive: They are essential for pneumatic tools, painting, and tire inflation in the automotive sector.
The rotary screw air compressor is a versatile and efficient tool widely used in industries for its continuous and reliable supply of compressed air. Its helical rotor design, low maintenance, and silent operation make it a preferred choice for various applications.
Rotary Vane Air Compressor
What is the Rotary Vane Air Compressor?
The rotary vane air compressor is a type of positive displacement compressor that utilizes vanes or blades mounted on a rotor to compress air.
As the rotor rotates, the vanes slide in and out of the rotor slots, creating compression chambers that draw in and compress the air. This continuous rotary motion allows for a consistent supply of compressed air with minimal pulsation.
How Does it Work?
In a rotary vane air compressor, the main components are the rotor, vanes, and the housing. The rotor is eccentrically mounted within the housing, and the vanes are free to move in and out of the rotor slots. As the rotor spins, centrifugal force pushes the vanes against the housing, creating a seal and trapping the air between the vanes.
As the rotor continues to rotate, the volume of the compression chambers decreases, leading to the compression of the air. Once the compressed air reaches the desired pressure, it is discharged through an outlet valve. The rotor’s design ensures that there is a continuous flow of air and that the compression process is efficient and reliable.
Advantages of Rotary Vane Air Compressors
Rotary vane air compressors offer several advantages that make them suitable for various applications:
Compact Design: They have a compact and space-efficient design, making them ideal for installations with limited space.
Smooth Operation: Rotary vane compressors provide a steady flow of compressed air with minimal vibration, resulting in smoother and quieter operation.
Energy Efficiency: The design and operation of rotary vane compressors contribute to their energy-efficient performance, helping to reduce operational costs.
Versatility: They can handle a wide range of air demands, making them suitable for various industrial applications.
Low Maintenance: With fewer moving parts and simpler construction, rotary vane compressors generally require lower maintenance compared to other types.
Industries Where Rotary Vane Air Compressors are Used
Due to their efficiency and reliability, rotary vane air compressors find application in various industries:
Manufacturing: They power pneumatic tools, air-operated machinery, and assembly lines in manufacturing facilities.
Woodworking: Rotary vane compressors are commonly used in woodworking shops for operating tools and equipment.
Printing: They provide the compressed air required for printing presses and related machinery.
Food and Beverage: Rotary vane compressors are used for packaging, labeling, and other processes in the food and beverage industry.
Pharmaceutical: They play a critical role in providing clean and compressed air for various pharmaceutical manufacturing processes.
Its unique rotary vane design ensures smooth and efficient compression of air, making rotary vane air compressor a popular choice for many applications.
Scroll Air Compressor
What is the Scroll Air Compressor?
The scroll air compressor is also a type of positive displacement compressor known for its simplicity, reliability, and efficiency.
It operates using two interleaved spiral scrolls, one fixed and the other orbiting, which create a series of crescent-shaped pockets. As the orbiting scroll moves, the pockets decrease in size, compressing the air trapped inside. This continuous movement generates a steady flow of compressed air without the need for valves
How Does it Work?
The working principle of the scroll air compressor is based on the relative movement between the fixed and orbiting scrolls.
When the orbiting scroll rotates, its spiral motion draws air into the compressor, and the pockets formed between the scrolls capture and compress the air.
As the orbiting scroll continues to move, the air is further compressed until it reaches the desired pressure. Finally, the compressed air is discharged from the center of the scrolls.
The scroll air compressor’s design eliminates the need for complex valve systems, resulting in reduced energy consumption and enhanced efficiency.
Additionally, the scroll compression process is oil-free, making it suitable for applications requiring clean and oil-free air, such as in the medical and pharmaceutical industries.
Advantages of Scroll Air Compressors
The scroll air compressor offers several advantages that make it a preferred choice in various applications:
Oil-Free Operation: Scroll compressors are inherently oil-free, ensuring high-quality compressed air without the risk of oil contamination.
Low Noise and Vibration: The continuous and smooth scroll movement results in quieter operation compared to other compressor types.
Energy Efficiency: Scroll compressors have a simple design with fewer moving parts, leading to reduced energy consumption and operating costs.
Reliability and Durability: With minimal wear and tear due to the absence of metal-to-metal contact, scroll compressors are known for their longevity and reliability.
Compact Size: The compact design of scroll compressors allows for easy installation and saves valuable floor space.
Industries Where Scroll Air Compressors are Used
Scroll air compressors find applications in various industries where clean, quiet, and reliable compressed air is required:
Medical and Healthcare: Scroll compressors are commonly used in medical air systems, dental equipment, and pharmaceutical manufacturing processes.
Laboratories: They provide oil-free and contaminant-free air for various laboratory applications.
Food and Beverage: Scroll compressors are utilized for food packaging, processing, and beverage dispensing systems.
Electronics: They are employed in the semiconductor and electronics industry, where clean and oil-free air is essential.
Home Appliances: Scroll compressors are used in air conditioners, refrigerators, and heat pumps for their quiet and efficient operation.
The scroll air compressor offers a reliable, energy-efficient, and oil-free solution for generating compressed air. Its unique design and advantages make it suitable for a wide range of industries, including medical, laboratory, food and beverage, electronics, and home appliances.
Rotary Screw Compressor VS Scroll Compressor
The debate between rotary compressors and scroll compressors has long been a topic of discussion. Both offer unique advantages and are widely used in various industries.
In this article, we will delve into the key differences and benefits of these two compressor types, helping you make an informed decision for your specific needs.
The above are several mainstream positive air compressor types. Next, we will continue to learn more about the types of dynamic air compressors.
Dynamic Air Compressor
What is the Dynamic Air Compressor?
The dynamic compressor is commonly used in applications where high volumes of compressed air are required. It works with high-speed rotating impellers to accelerate the air and then convert the kinetic energy into pressure.
What types of air compressors does it include?
There are two main types of dynamic air compressors:
- Centrifugal Air Compressor
- Axial Air Compressor
Let’s explore more.
Centrifugal Air Compressor
What is the Centrifugal Air Compressor?
The centrifugal air compressor is a type of dynamic compressor known for its high flow rates and continuous operation.
Unlike positive displacement compressors, which trap and reduce the air volume, the centrifugal compressor works on the principle of converting kinetic energy into pressure energy to compress the air.
It is widely used in various industries for its efficiency, reliability, and ability to handle large volumes of compressed air.
How Does it Work?
The centrifugal air compressor operates using a rotating impeller that accelerates the incoming air to high speeds. The impeller, housed in a diffuser or volute casing, converts the kinetic energy of the air into pressure energy.
As the air passes through the impeller’s blades, it gains velocity and is directed towards the diffuser, where the kinetic energy is converted into pressure energy. This process significantly increases the air pressure, producing compressed air at the outlet.
Advantages of Centrifugal Air Compressors
High Flow Rates: Centrifugal compressors are designed to handle large volumes of air, making them suitable for applications requiring high flow rates.
Energy Efficiency: The isentropic compression process of centrifugal compressors results in energy-efficient operation, reducing power consumption and operational costs.
Oil-Free Air: Centrifugal compressors are inherently oil-free, making them ideal for applications where clean, oil-free air is essential, such as in the electronics and food industries.
Low Maintenance: With fewer moving parts and no reciprocating components, centrifugal compressors require less maintenance and have longer service intervals.
Continuous Operation: Centrifugal compressors can operate continuously without the need for frequent starts and stops, providing a stable and constant supply of compressed air.
Industries Where Centrifugal Air Compressors are Used
Petrochemical and Refining: Centrifugal compressors are used in petrochemical plants for various processes like gas compression and refrigeration.
Power Generation: They play a crucial role in power plants for air separation, combustion air, and gas turbine operations.
HVAC and Refrigeration: Centrifugal compressors are used in large-scale HVAC systems, chillers, and refrigeration units.
Manufacturing: Industries like automotive, steel, and textiles use centrifugal compressors for various pneumatic tools and processes.
Aerospace: They are utilized in aviation for aircraft pressurization and environmental control systems.
In conclusion, the centrifugal air compressor is a dynamic and efficient compressor widely used in various industries for its high flow rates, energy efficiency, and reliability. Its ability to provide clean, oil-free compressed air makes it suitable for applications requiring a continuous and stable air supply.
Axial Air Compressor
What is the Axial Air Compressor?
The axial air compressor is a rotating machine that utilizes a series of axial-flow stages to compress air. Each stage consists of rows of blades mounted on rotating and stationary discs.
The airflow moves parallel to the compressor axis. This design allows for continuous and smooth compression of air, making axial compressors efficient for various applications.
How Does it Work?
The axial compressor works based on the aerodynamic principle of converting kinetic energy into pressure energy.
When the compressor’s rotor blades rotate, they impart velocity to the incoming air, causing it to move in an axial direction. The stationary stator blades guide the airflow and further increase its velocity. As the air moves through each stage, the combination of rotating and stationary blades accelerates and compresses the air, resulting in a higher-pressure output.
Advantages of Axial Air Compressors
High Efficiency: Axial compressors are known for their high efficiency in converting kinetic energy into pressure energy, making them energy-efficient and cost-effective.
Compact Design: The axial compressor’s compact design allows for easy installation and integration into various systems, saving valuable space.
High Flow Rates: Axial compressors can handle large volumes of air, making them suitable for applications where a continuous and substantial air supply is required.
Low Maintenance: With fewer moving parts compared to other compressor types, axial compressors require less maintenance and have longer service intervals.
Versatility: Axial compressors are used in both low-pressure and high-pressure applications, showcasing their versatility in various industries.
Industries Where Axial Air Compressors are Used
Aviation: Axial compressors are widely used in aircraft engines for their high-pressure ratios and efficiency, contributing to aircraft propulsion.
Power Generation: They play a crucial role in gas turbine power plants for electricity generation.
Oil and Gas: Axial compressors are utilized in the oil and gas industry for gas compression and transportation.
HVAC and Refrigeration: They are used in large-scale air conditioning systems, chillers, and refrigeration units.
In Conclusion
There are many types of air compressors, the above are the mainstream air compressors on the market.
Depending on the usage scenarios and applications, they all have different advantages:
For small application scenarios, such as home use, air tools, nail guns, printing, etc., reciprocating air compressors are widely used.
For industrial applications, such as machine processing, food and beverage, mining, etc., large centrifuges and rotary screw air compressors are almost the first choice.
Special scenes such as pharmaceutical and textile industries have very high requirements on air quality, the oil-free rotary screw air compressor can fully meet your needs.
In addition, for buyers who are energy-conscious, variable speed rotary screw air compressors have been proven to save your business a lot of electricity consumption.