Diesel Air Compressor in Oil and Gas Indsutry
Whether they are stationary or mobile diesel air compressors, they are indispensable in the oil and gas industry.
How to Solve Two Pain Points of Diesel Air Compressor in Oil and Gas Industry?
High Temperature
In hot areas such as the GCC Countyies, Mexico, and Brazil, diesel compressors require more efficient water cooling methods and are equipped with intercoolers.
Continuous Operation
In the oil and gas industry, it is common for air compressors to operate continuously for 4-5 months. This requires a more stable and reliable diesel engine and screw rotor.
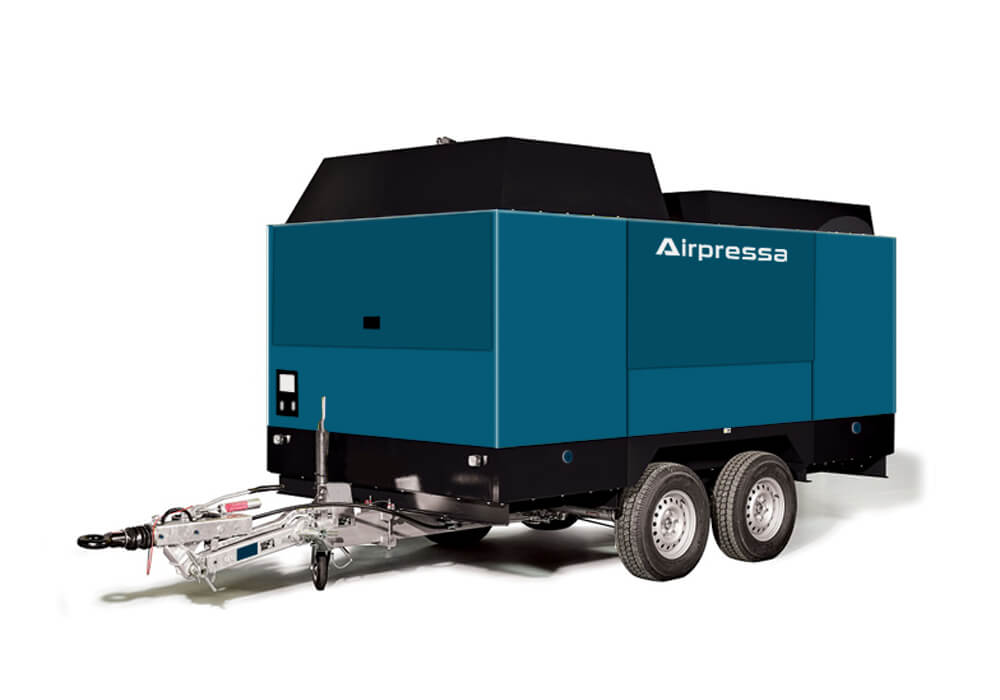
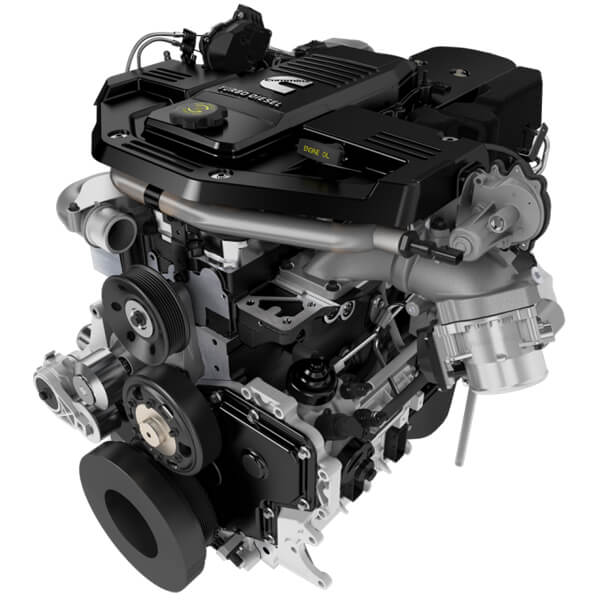
Cummins Diesel Engine
Reliability: Cummins engines are known for their durability and reliability, making them suitable for various applications and operating conditions.
Fuel Efficiency: Cummins engines are designed to deliver excellent fuel efficiency, helping to reduce operating costs over the long term.
Power and Performance: Cummins engines offer impressive power and performance, providing ample torque and horsepower for demanding tasks.
Durability: With robust construction and high-quality materials, Cummins engines are built to withstand harsh environments and heavy-duty use.
Low Emissions: Cummins engines are designed to meet stringent emissions regulations, offering environmentally friendly operation.
Twin Rotary Screw Air End
Airpessa’s rotary screw air end uses an industry-leading screw air end with a low rotating speed.
Efficiency: Airpressa’s screw air end is highly efficient, delivering maximum compressed air output while minimizing energy consumption.
Reliability: With robust construction and precision engineering, Airpressa’s screw air end ensures reliable and continuous operation even in demanding industrial environments.
Performance: The screw air end from Airpressa offers superior performance, providing consistent and stable compressed air supply for oil & gas industry.
Durability: Built to withstand heavy-duty use, Airpressa’s screw air end is durable and long-lasting, reducing maintenance requirements and downtime.
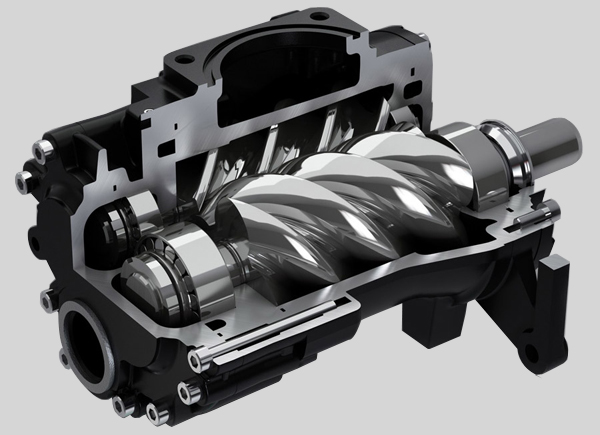
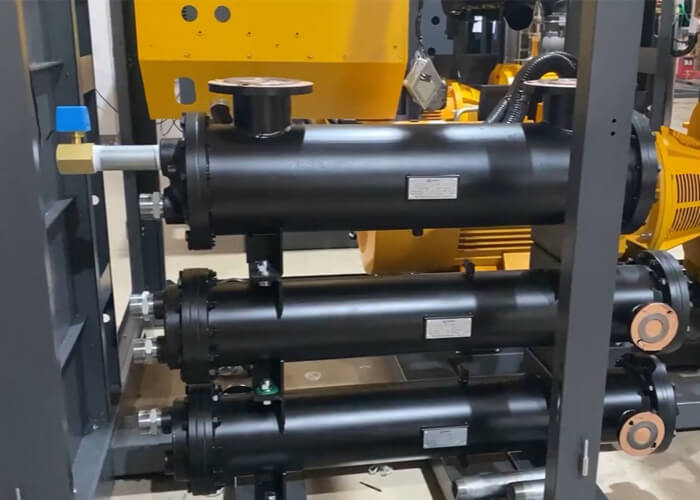
Water Cooling System
Better in High Ambient Temperatures
Water’s high heat absorption capacity allows it to cool the compressor parts more effectively than air. When outdoor temperatures soar, the efficiency of air-cooled compressors can falter, leading to infrequent output consistency.
Meanwhile, water-cooled compressors tend to maintain a stable level of performance because their cooling efficiency isn’t affected by ambient temperature fluctuations.
More Suitable for Continuous Work
Water-cooled system let Airpressa’s compressors are better suited for continuous-duty applications in hot environments. The efficient cooling mechanism allows these compressors to maintain consistent performance levels over extended operating periods without the risk of overheating.
AIRPRESSA Diesel Air Compressor 530 CFM
A | Comperssor | |
1 | Free Air delivery | 15 m3/min (530 CFM) |
2 | Rated Operating Pressure KG/Cm2 ( PSIG) (Kpa) | 145 PSIG (10 bar) |
3 | Recevier Tank Capacity m3 | 2.64 US Gal (10 L) |
4 | Air Outlets | 4 Air Outlets (G1, G1, G2 G2) |
B | Engine | |
1 | Make & Model | Cummins QSB5.9-C190-31 |
2 | Type ( Cycle, Water/Air Coolant, Injection/Turbo Charge) | 6 Cycle, Water Coolant, Turbo Charge |
3 | No. Of Cylinder | 4 |
4 | Total Displacement cc | 5900 |
5 | Rated OUTPUT PS(KW)/RPM | 190 HP (142KW) / 2500r/min |
6 | Fuel tak Capacity Liters | 52.8 US Gal (200 L) |
7 | Lubircation Oil Capacity Liters | 4.5 US Gal (17 L) |
C | Dimension | |
Overall Length ( Inch) | 94.5 | |
Overall Width (Inch) | 68.9 | |
Overall Height (Inch) | 78.74 | |
Weight (DRY) KG (lb) | 2200 KGS (4850 lbs) | |
Weight (Wet) KG (lb) | 2500 KGS (5512 lbs) | |
Tire Size | 15 inch | |
Type of Mounting ( I.e Nos of wheel) | 4 wheels (or stationary) |
AIRPRESSA Diesel Air Compressor 850 CFM
A | Comperssor | |
1 | Free Air delivery | 24 m3/min (850 CFM) |
2 | Rated Operating Pressure KG/Cm2 ( PSIG) (Kpa) | 145 PSIG (10 bar) |
3 | Recevier Tank Capacity m3 | 2.64US Gal (10 L) |
4 | Air Outlets | 4 Air Outlets (G1, G1, G2 G2) |
B | Engine | |
1 | Make & Model | Cummins QSB5.9-C220-30 |
2 | Type ( Cycle, Water/Air Coolant, Injection/Turbo Charge) | 6 Cycle, Water Coolant, Turbo Charge |
3 | No. Of Cylinder | 4 |
4 | Total Displacement cc | 5900 |
5 | Rated OUTPUT PS(KW)/RPM | 220 HP (164KW) / 2200r/min |
6 | Fuel tak Capacity Liters | 52.8 US Gal (200 L) |
7 | Lubircation Oil Capacity Liters | 5.3 US Gal (20 L) |
C | Dimension | |
Overall Length ( Inch) | 94.5 | |
Overall Width (Inch) | 68.9 | |
Overall Height (Inch) | 78.74 | |
Weight (DRY) KG (lb) | 3100 KGS (6834 lbs) | |
Weight (Wet) KG (lb) | 3400 KGS (7496 lbs) | |
Tire Size | 15 inch | |
Type of Mounting ( I.e Nos of wheel) | 4 wheels (or stationary) |
Airpressa Provide Diesel Air Compressors for 185, 375, 530, 850, 1200, 1500 2000 CFM
They are suitable for many industries, include oil and gas, drilling, mining etc.
GET TECHNOLOGY SUPPORT & PRICES
Diesel compressors play a crucial role in the oil and gas industry, especially under demanding conditions such as high temperatures and continuous operation.
1. Well Testing: Diesel compressors are used for well testing operations in oil and gas fields. They help in extracting and measuring the flow rate, pressure, and composition of the fluids produced from the well.
2. Gas Gathering: In gas gathering systems, diesel compressors are employed to compress natural gas from wellheads and transport it through pipelines to processing plants or storage facilities.
3. Pipeline Maintenance: Diesel compressors are used for pipeline maintenance tasks such as cleaning, purging, and pressurizing pipelines to detect leaks or perform repairs.
4. Well Stimulation: Diesel compressors are utilized in well stimulation operations, including hydraulic fracturing (fracking), to inject fluids or gases into the wellbore at high pressure to enhance production.
5. Instrument Air: Diesel compressors provide instrument air for pneumatic control systems, safety devices, and instrumentation used in oil and gas processing facilities.
6. Offshore Platforms: On offshore drilling rigs and production platforms, diesel compressors power various equipment and machinery, including pneumatic tools, controls, and safety systems.
7. Emergency Backup: Diesel compressors serve as reliable backup power sources during emergencies or power outages, ensuring continuous operation of critical equipment and safety systems.
To ensure a diesel compressor can adapt to the high temperature and continuous operation characteristics of the oil and gas industry, it should be designed with several key features:
1. Robust Construction: The compressor should have a durable and rugged construction using high-quality materials that can withstand harsh environmental conditions, including high temperatures, humidity, and corrosion.
2. Efficient Cooling System: A robust cooling system is essential to dissipate heat generated during compression efficiently. This may involve incorporating larger radiators, cooling fans, or even liquid cooling systems to maintain optimal operating temperatures.
3. Heat Resistant Components: Components such as pistons, cylinders, valves, and seals should be made from heat-resistant materials capable of withstanding prolonged exposure to high temperatures without degradation or failure.
4. Advanced Filtration: Effective air and oil filtration systems are necessary to prevent contaminants from entering the compressor and causing damage to internal components, particularly in dusty or sandy environments common in the oil and gas industry.
5. Enhanced Lubrication System: A reliable lubrication system with high-quality oils and filters is crucial for reducing friction, minimizing wear, and maintaining the performance and longevity of the compressor’s moving parts, especially under continuous operation.
6. Automatic Shutdown and Safety Features: Diesel compressors should be equipped with automatic shutdown and safety features to protect against overheating, overloading, low oil pressure, and other potential hazards. These safety mechanisms help prevent equipment damage and ensure personnel safety.
7. Remote Monitoring and Control: Incorporating remote monitoring and control capabilities allows operators to monitor the compressor’s performance, diagnose issues, and adjust settings remotely, minimizing downtime and improving operational efficiency.
8. Comprehensive Maintenance Plan: Implementing a comprehensive maintenance plan that includes regular inspections, preventive maintenance, and timely repairs is essential for ensuring the continued reliability and efficiency of the diesel compressor under high-temperature and continuous operation conditions.
By incorporating these design considerations, diesel compressors can be engineered to meet the rigorous demands of the oil and gas industry, delivering reliable performance and durability even in the most challenging operating environments.
