Home » Industries »
Air Compressor for Injection Molding
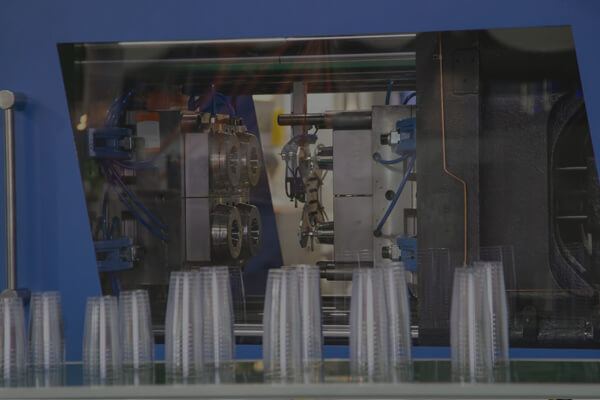
Air Compressor Used in Injection Molding Industry
Injection molding is a manufacturing process used to produce intricate parts by injecting molten material into a mold cavity under high pressure. Throughout this process, compressed air serves various essential functions, such as powering pneumatic actuators, cooling molds, and ejecting finished parts.
How is Air Compressor Used in the Injection Molding Industry
Air compressors are indispensable components in the injection molding industry, serving a variety of critical functions to ensure the success of the manufacturing process.
Powering Pneumatic Actuators
Injection molding machines utilize pneumatic actuators to control various functions such as opening and closing molds, ejecting finished parts, and operating robotic arms.
Air compressors provide the necessary compressed air to power these actuators, enabling precise and reliable movement during the molding cycle.
Cooling Molds
Effective mold cooling is essential for achieving high-quality molded parts and optimizing cycle times. Air compressors supply compressed air to cooling circuits within the molds, facilitating rapid heat transfer and ensuring uniform cooling of the molten material.
This helps prevent defects such as warping, shrinkage, and uneven cooling, resulting in consistent part dimensions and surface finish.
Blow-off and Cleaning
Compressed air is used for blow-off and cleaning operations to remove excess material, debris, or contaminants from molds, tools, and machinery. High-pressure air jets generated by air compressors help maintain cleanliness and prevent buildup that could affect the quality of molded parts or disrupt production processes.
Material Handling
In injection molding facilities, air compressors are often employed to power pneumatic conveying systems used for transporting raw materials, additives, or finished parts within the production area.
These systems rely on compressed air to create airflow, enabling the efficient transfer of materials between different stages of the manufacturing process.
Auxiliary Equipment
Air compressors also support the operation of auxiliary equipment such as hopper dryers, mold temperature controllers, and hot runner systems. These devices may require compressed air for actuation, temperature regulation, or process control, contributing to the overall efficiency and performance of the injection molding process.
How to Select the Right Air Compressor for Injection Molding
Selecting the right air compressor for injection molding operations is essential to ensuring efficient production processes, maintaining product quality, and minimizing downtime.
By considering factors such as oil-free operation, pressure output, control mechanisms, reliability, and air treatment capabilities, manufacturers can optimize their injection molding processes and achieve superior results.
Rotary Screw Compressor
In injection molding applications, rotary screw compressors are preferred for their reliability, efficiency, and ability to deliver a continuous supply of compressed air.
These compressors operate on the principle of rotary motion, where two interlocking helical rotors compress the air as it moves through the compressor. This design ensures smooth and consistent airflow, which is essential for maintaining stable pressure during the injection molding process.
Oil-Free Screw Compressors
Oil free compressors are often preferred for injection molding applications due to their ability to deliver clean and contaminant-free air. They eliminate the risk of oil contamination, ensuring the quality and integrity of the molded products.
The Ultimate Guide: What Is The Oil-free Air Compressor?
The oil-free air compressor is one of the most popular types of air compressors. It plays a vital role in many industries and manufacturers. Click to delve into the world of oil-free air compressors and explore their benefits, applications, and maintenance requirements.
High Pressure Output
Injection molding operations often require compressed air at high pressures to facilitate the mold cooling process effectively.
Therefore, selecting a compressor capable of delivering sufficient pressure is crucial to maintaining optimal mold temperatures and achieving desired part quality.
Variable Speed Drive (VSD) Technology
For injection molding processes that require varying air demands, such as those with fluctuating production cycles or different mold sizes, rotary screw compressors equipped with Variable Speed Drive (VSD) technology are highly beneficial.
VSD compressors automatically adjust their motor speed to match the air demand, ensuring energy efficiency and reducing operational costs.
What is the VSD Compressor and How to Choose Correctly
VSD compressor is a cutting-edge technology that has gained significant traction in recent years.
These advanced compressors have revolutionized the way compressed air is generated, offering unmatched energy-saving capabilities, flexibility, and control.
The VSD compressor has become a game-changer in the field of air compression, powering the modern-day industry. But what exactly is a VSD compressor, and how do you choose the right one for your business?
Reliability and Durability
Injection molding processes are typically continuous and demanding, requiring air compressors with robust construction and reliable performance. Investing in high-quality, industrial-grade compressors ensures uninterrupted operation and minimizes downtime.
Integrated Air Treatment Systems
In injection molding applications, the quality of compressed air is paramount to prevent contamination of molds and finished products.
Integrated air treatment systems, including air dryers and compressed air filters, help remove moisture, oil, and other contaminants, ensuring the purity of compressed air and the integrity of the molding process.
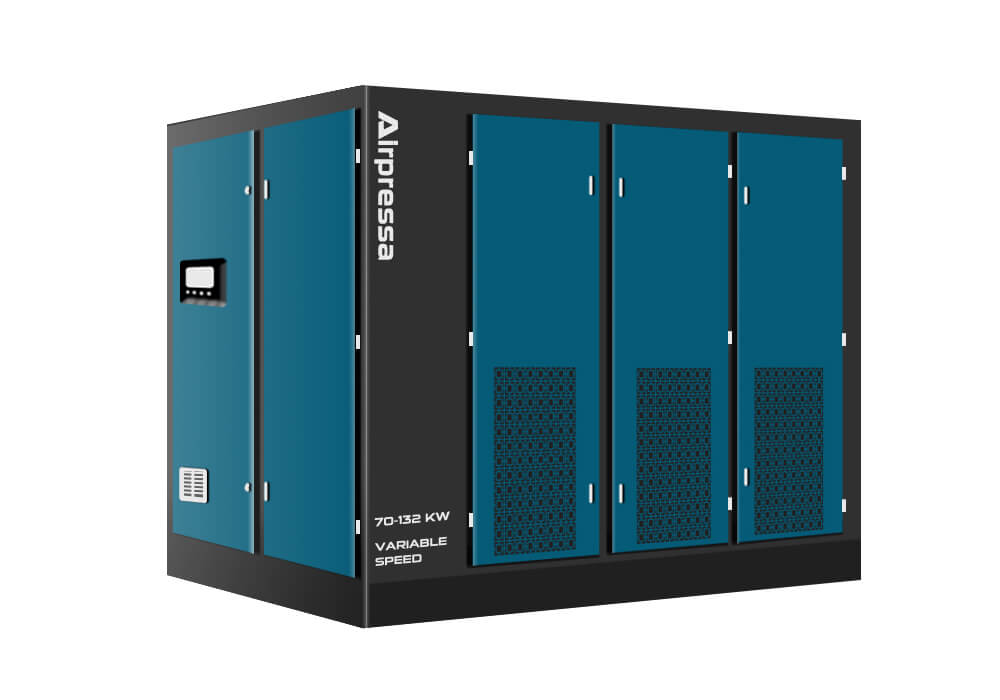
Variable Speed Compressors
By employing variable speed drive technology, these compressors optimize energy consumption by adjusting the motor’s speed according to the air demand.
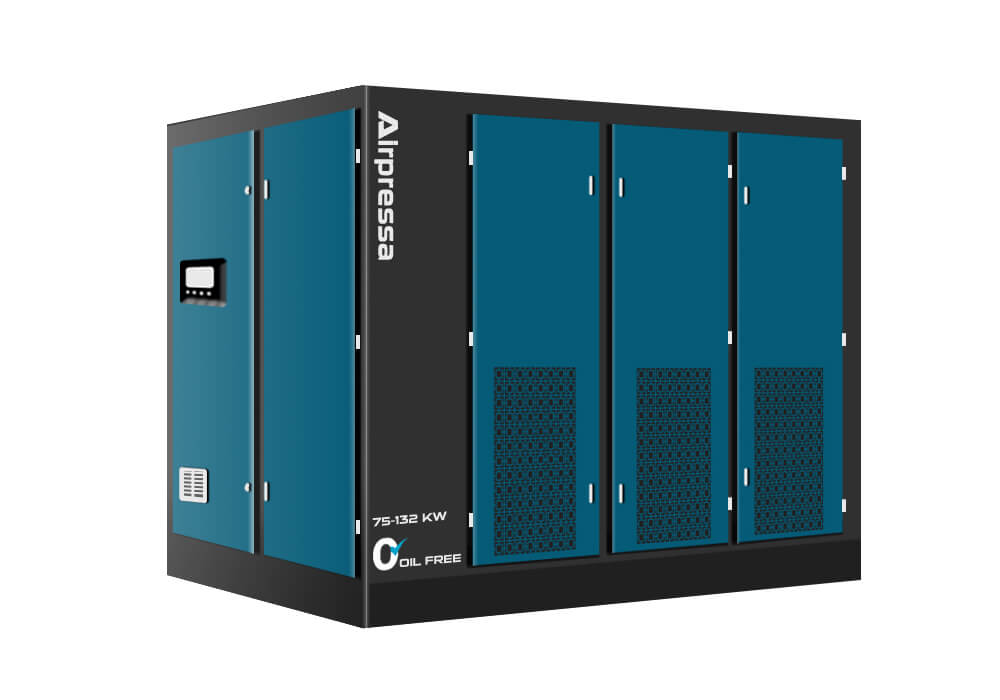
Oil-free Compressors
Oil free air compressors provide high-quality compressed air free from oil contamination, ensuring the integrity of sensitive processes and applications.
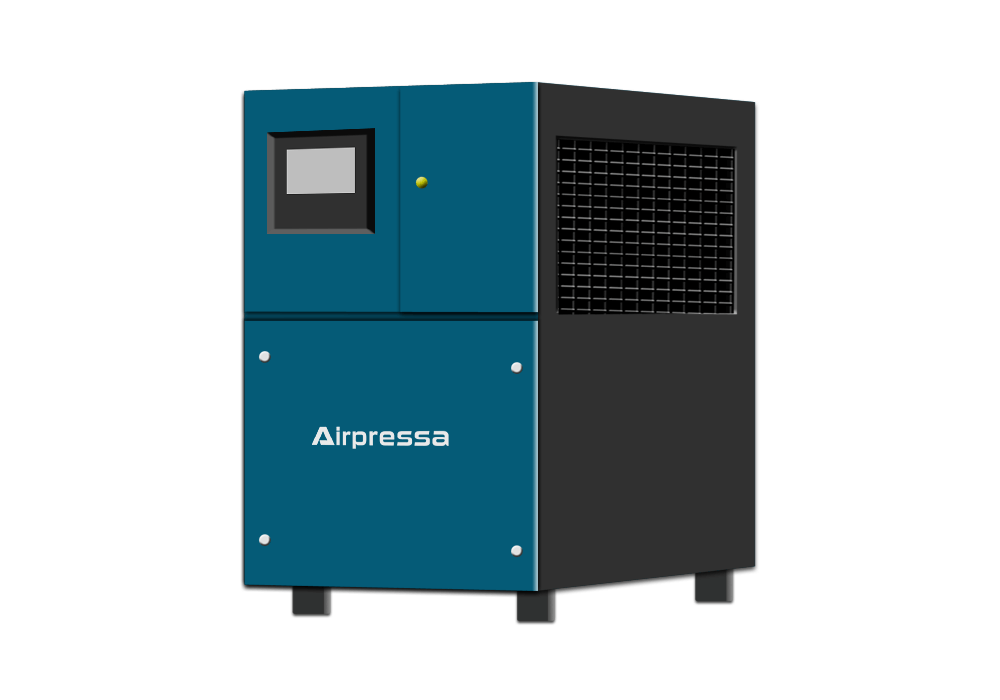
Refrigerated Air Dryers
Air dryers are responsible for removing moisture and contaminants, ensuring clean and dry air for various applications.
How Much CFM, Bar/PSI of Air Compressor Should I Choose?
Consider Air Consumption
Start by evaluating the air consumption of your injection molding machines and associated equipment. Calculate the total air demand during peak production periods, including pneumatic actuators, cooling circuits, blow-off systems, and auxiliary machinery.
Determine Operating Pressure
Identify the optimal operating pressure for your injection molding process. This will depend on factors such as the type of molds, material viscosity, part complexity, and cycle time.
While most injection molding applications typically require air pressures in the range of 80 to 120 psi (5.5 to 8.3 bar), certain specialized processes may demand higher or lower pressures.
Convert m3/min to cfm chart
Account for Pressure Drop
Factor in pressure drop considerations due to piping, filters, regulators, and other components in the air distribution system. Ensure that the selected air compressor can deliver sufficient pressure at the point of use, compensating for any pressure losses along the distribution network.
Size for Future Growth
Anticipate future growth and expansion of your injection molding operation when sizing the air compressor.
Invest in a compressor with sufficient capacity to accommodate increased air demand as your production needs evolve. Oversizing the compressor slightly can provide a buffer for potential growth without sacrificing efficiency.
Get Expert Support
Choose Airpressa for all your compressed air needs and experience the benefits of working with a reliable, professional, and customer-focused manufacturer.